The Scientific Research Behind Porosity: A Comprehensive Overview for Welders and Fabricators
Understanding the complex systems behind porosity in welding is essential for welders and fabricators pursuing impressive craftsmanship. As metalworkers look into the depths of this phenomenon, they uncover a globe governed by various elements that influence the development of these minuscule gaps within welds. From the structure of the base materials to the complexities of the welding procedure itself, a wide variety of variables conspire to either worsen or ease the existence of porosity. In this extensive guide, we will certainly untangle the science behind porosity, discovering its impacts on weld quality and introduction progressed techniques for its control. Join us on this journey through the microcosm of welding blemishes, where precision fulfills understanding in the search of remarkable welds.
Comprehending Porosity in Welding
FIRST SENTENCE:
Exam of porosity in welding reveals critical insights right into the integrity and quality of the weld joint. Porosity, identified by the existence of dental caries or voids within the weld metal, is an usual issue in welding processes. These voids, if not effectively addressed, can jeopardize the structural stability and mechanical residential properties of the weld, bring about potential failures in the completed product.

To detect and evaluate porosity, non-destructive testing methods such as ultrasonic screening or X-ray evaluation are frequently used. These techniques permit for the identification of internal issues without compromising the honesty of the weld. By assessing the dimension, shape, and circulation of porosity within a weld, welders can make educated decisions to boost their welding processes and accomplish sounder weld joints.

Variables Affecting Porosity Formation
The event of porosity in welding is influenced by a myriad of elements, varying from gas shielding performance to the ins and outs of welding criterion settings. Welding specifications, consisting of voltage, existing, travel rate, and electrode kind, also effect porosity development. The welding strategy used, such as gas metal arc welding (GMAW) or shielded steel arc welding (SMAW), can affect porosity formation due to variations in warm circulation and gas insurance coverage - What is Porosity.
Effects of Porosity on Weld Top Quality
The presence of porosity also weakens the weld's resistance to deterioration, as the entraped air or gases within the spaces can react with the surrounding setting, leading to deterioration over time. In addition, porosity can hinder the weld's ability to hold up against stress or impact, further threatening the general quality and reliability of the bonded structure. In vital applications such as aerospace, automotive, or structural buildings, where safety and security and durability are extremely important, the harmful results of porosity on weld quality can have serious effects, highlighting the relevance of reducing porosity through correct welding methods and treatments.
Strategies to Reduce Porosity
In addition, using the appropriate welding specifications, such as the proper voltage, existing, and take a trip rate, is vital in preventing porosity. Preserving a constant arc length and angle throughout welding likewise aids lower the likelihood of porosity.

Furthermore, picking the right shielding gas and maintaining proper gas flow rates are essential in minimizing porosity. Using the ideal welding strategy, such as back-stepping or using a weaving motion, can likewise aid distribute heat equally and lower the possibilities of porosity formation. Guaranteeing proper air flow in the welding atmosphere to get rid of any kind of possible sources of contamination is essential for accomplishing porosity-free welds. By executing these strategies, welders can properly lessen porosity and generate top quality welded joints.
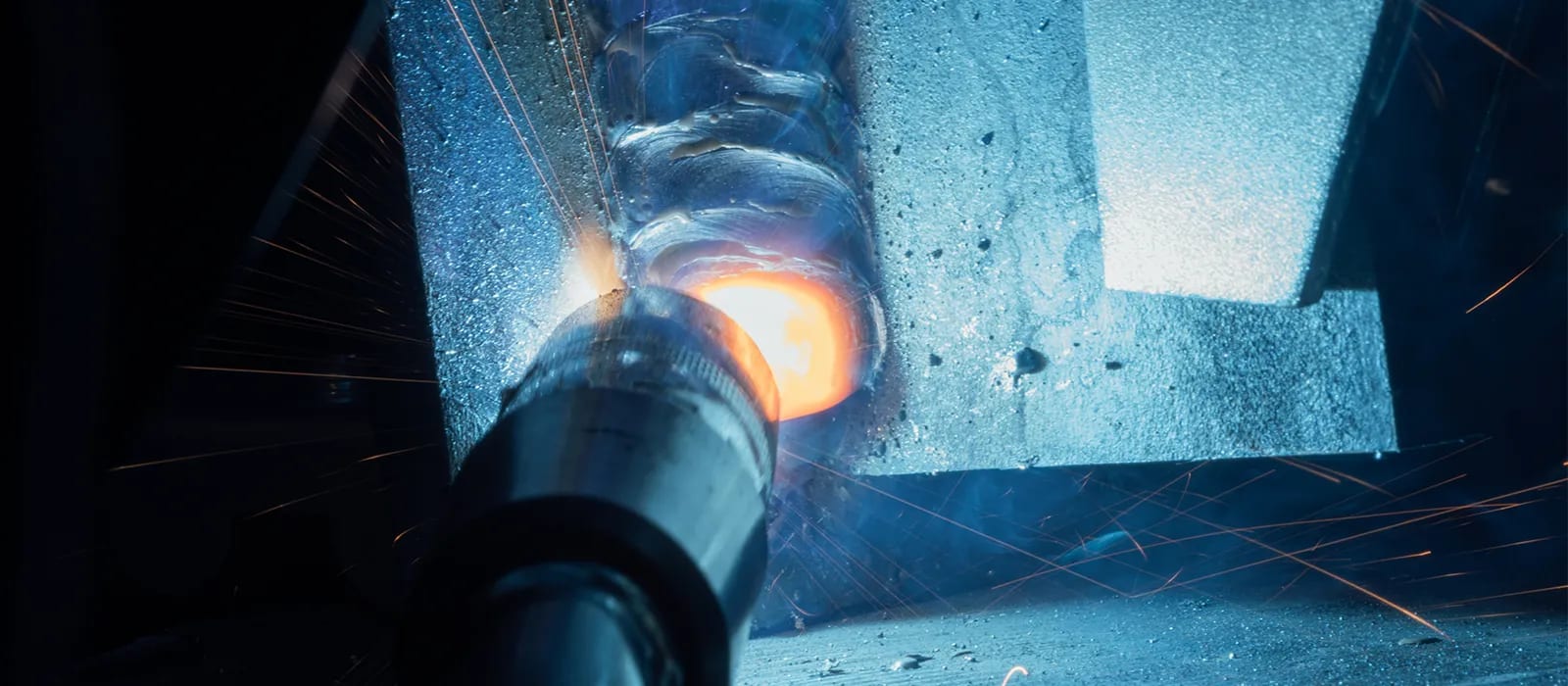
Advanced Solutions for Porosity Control
Implementing sophisticated innovations and ingenious approaches plays an essential function in accomplishing exceptional control over porosity in welding procedures. additional hints One sophisticated solution is the use of advanced gas blends. Shielding gases like helium or a mixture of argon and hydrogen can assist minimize porosity by offering far better arc stability and boosted gas insurance coverage. Additionally, using innovative welding techniques such as pulsed MIG welding or customized ambience welding can also aid reduce porosity problems.
Another sophisticated option entails making use of innovative welding tools. Making use of devices with built-in functions like waveform control and innovative power sources can boost weld top quality and decrease porosity dangers. The execution of automated welding systems with specific control over parameters can considerably minimize porosity defects.
Furthermore, integrating go to this web-site innovative monitoring and assessment innovations such as real-time X-ray imaging or automated ultrasonic visit this site screening can aid in spotting porosity early in the welding procedure, permitting for immediate corrective actions. Overall, incorporating these innovative solutions can significantly improve porosity control and enhance the overall top quality of bonded components.
Verdict
In verdict, comprehending the scientific research behind porosity in welding is important for welders and fabricators to generate premium welds - What is Porosity. Advanced remedies for porosity control can better improve the welding process and ensure a solid and trusted weld.
Comments on “What is Porosity in Welding: Comprehending Its Causes and Enhancing Your Skills”